La gestión de la producción es un conjunto de actividades y procesos que permiten planificar, coordinar y controlar los recursos necesarios para optimizar la fabricación en las empresas.
En este post os contaremos qué se entiende por gestión de la producción detallando funcionalidades, cuáles son los objetivos de la gestión de la producción industrial así como los software más adecuados para llevar dicha gestión de la producción a buen puerto.
¿Qué es la gestión de la producción?
La gestión de la producción es un conjunto de actividades y procesos que se encargan de planificar, coordinar y controlar todas las etapas y recursos necesarios para la fabricación de manera eficiente y efectiva. El objetivo es que una determinada materia prima llegue a ser un producto acabado listo para su comercialización, considerando en todo momento la eficiencia de la producción.
Se centra principalmente en optimizar los recursos disponibles, como el tiempo, la mano de obra, los materiales y la maquinaria, garantizando que los productos se elaboren en la cantidad y calidad requeridas con el menor costo posible.
La gestión de la capacidad productiva abarca una variedad de funciones, que permiten identificar aspectos generales y esenciales que definen lo que se debe lograr, las más destacadas son:
Planificación: esto implica determinar qué productos se fabricarán, en qué cantidad y cuándo se producirán. Se deben considerar factores como la demanda del mercado, la capacidad de producción y la disponibilidad de recursos.
Organización: se refiere a la asignación de responsabilidades, recursos y autoridad para llevar a cabo los planes de producción. Esto incluye la toma de decisiones, la solución de problemas y la comunicación efectiva.
Dirección: implica liderar y motivar a los equipos de producción para que cumplan con los objetivos. Esto incluye la toma de decisiones, la solución de problemas y la comunicación efectiva que realizará el director de producción o manager de operaciones.
Control: supervisa y asegura que la producción se desarrolle según lo planificado. Se realizan mediciones, se comparan con los estándares y se toman acciones correctivas si es necesario.
Coordinación: coordinar es hacer que todas las piezas del rompecabezas encajen. Esta función se encarga de asegurar que todos los procesos y recursos trabajen juntos de manera armoniosa.
Mejora continua: es una característica esencial de la gestión de la producción. Implica la búsqueda constante de formas de hacer las cosas mejor, más eficientemente y a menor costo.
En estos aspectos es clave la implicación de gerencia, para que la gestión empresarial y la gestión industrial trabajen al unísono y no de forma independiente.
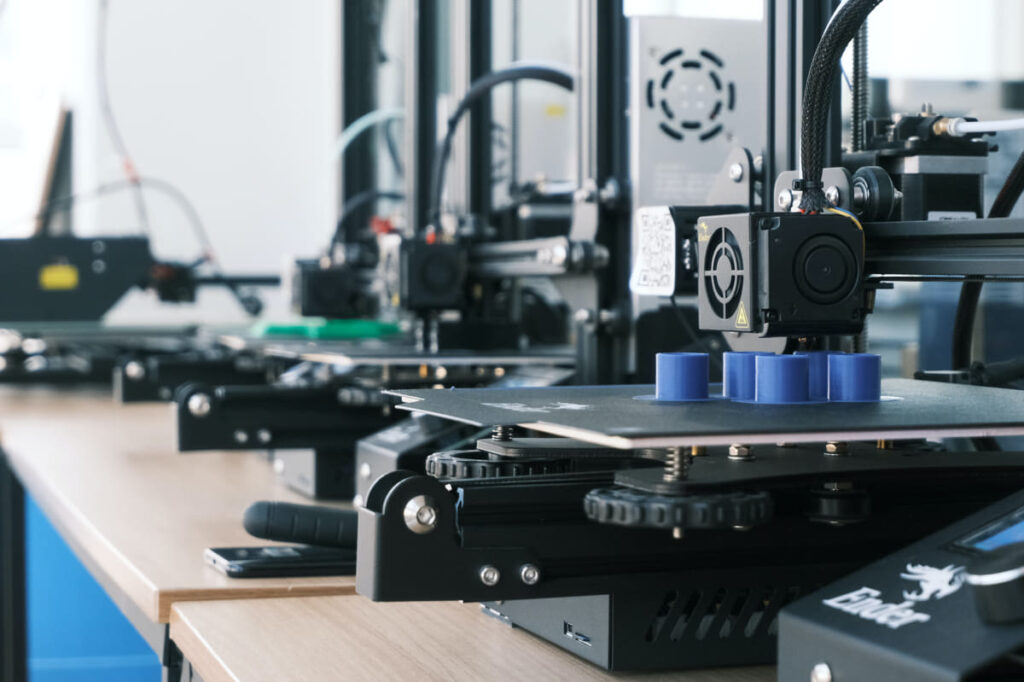
Objetivos de la Gestión de la Producción Industrial
Los objetivos de la gestión de la producción o principios de la gestión de la producción son fundamentales para el éxito a largo plazo de cualquier empresa. Los diferentes objetivos mencionados a continuación buscan impulsar la eficiencia, la calidad y la rentabilidad de la producción.
Los objetivos más destacados en la gestión de la producción industrial son:
1.- Optimización de recursos o eficiencia de la producción
Este es el objetivo prioritario dentro de la gestión de la producción, ya que lo que se persigue es utilizar los recursos disponibles (mano de obra, maquinaria, materiales, tiempo,…) de la manera más eficiente posible. Esto incluye también minimizar el desperdicio y maximizar la productividad.
Se busca aprovechar al máximo la capacidad de producción de la organización, de modo que se pueda producir más con los mismos recursos o, alternativamente, producir la misma cantidad con menos recursos.
2.- Mejora continua y de la calidad
Con la gestión de la producción se busca disponer de herramientas de mejora continua en todos los aspectos de la producción. Lo que implica la identificación y corrección constante de problemas y la implementación de mejores prácticas.
Además, es muy importante garantizar que la producción cumpla con los estándares de calidad requeridos. Lo que implica la implementación de controles de calidad, la prevención de defectos y la corrección de problemas cuando surgen.
3.- Reducción de costos
Uno de los objetivos clave es minimizar los costos de producción sin comprometer la calidad final del producto. Esto se puede lograr a través de la optimización de procesos, la gestión de inventarios eficiente y la reducción de desperdicio.
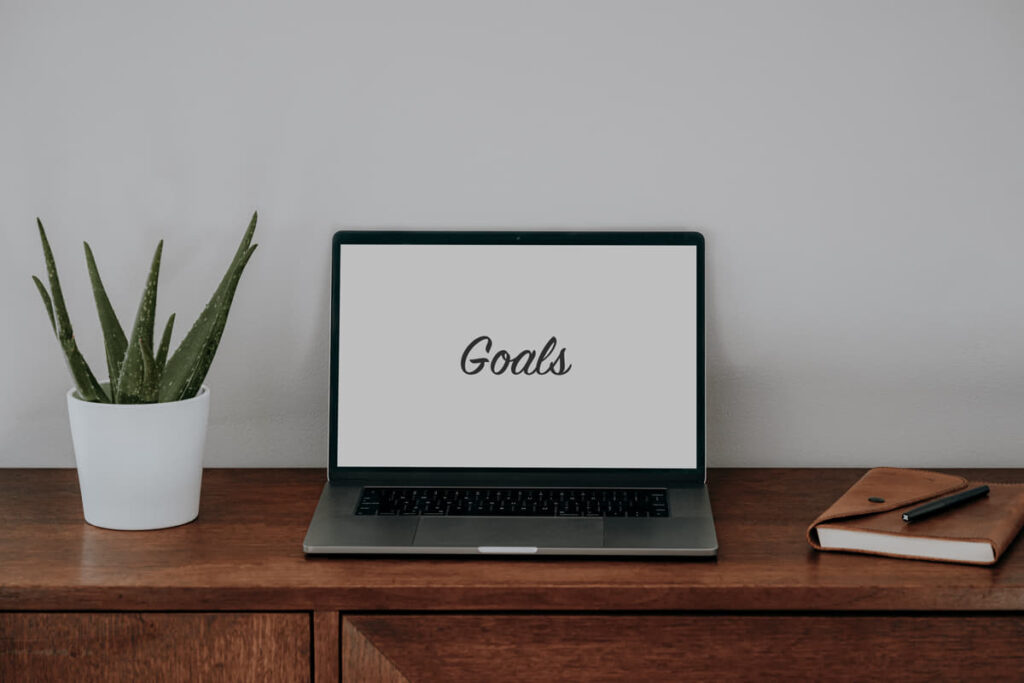
4.- Satisfacción del cliente
La satisfacción del cliente es un aspecto crítico dentro de cualquier organización, ya que es clave satisfacer las necesidades y expectativas de los clientes. Lo que implica entregar productos o servicios con alta calidad, a tiempo y a precios competitivos.
Por ello, el cumplimiento de los plazos establecidos en la entrega es uno de los pilares de la gestión de la producción, ya que se encarga de programar y controlar las operaciones para cumplir los plazos de entrega con el cliente.
5.- Flexibilidad y adaptabilidad
La gestión de la producción debe permitir a la organización adaptarse a los cambios en la demanda del mercado o a situaciones imprevistas, como interrupciones en la cadena de suministro. La flexibilidad es esencial para mantener la agilidad en la producción y dar un servicio satisfactorio a cada cliente. Esto es especialmente relevante en la gestión de la producción en fabricación mecánica.
6.- Gestión de riesgos
La identificación de riesgos, que afectan a la producción, de forma proactiva es un aspecto muy relevante dentro de la gestión de la producción. Esto se refiere a problemas en la cadena de suministro, cambios en la demanda del mercado o desastres naturales.
Procedimientos de la gestión de la producción
Los procedimientos son las acciones específicas que se llevan a cabo para implementar las funciones anteriormente mencionadas. Juegan un papel crucial en la gestión de la producción y contribuyen a garantizar la optimización de la producción. La implementación efectiva de estos procedimientos es esencial para el éxito continuo de una organización en su proceso de producción.
1.- Planificación avanzada de la producción
Para planificar adecuadamente la producción se consideran dos aspectos esenciales:
Plan Maestro de Producción (PMP) donde se establece cuánto se va a producir y cuándo. El PMP se basa en las demandas del mercado y las capacidades de producción de la empresa.
Programación de la Producción. Una vez que se tiene el Plan Maestro de Producción, se debe desglosar en un calendario detallado que especifique las tareas a realizar, los recursos necesarios y los plazos. Con el objetivo de que las actividades se coordinen eficazmente, asignando recursos y tiempos de producción de manera efectiva.
2.- Control de calidad
En el control de calidad se deben establecer estándares y controles de calidad para garantizar que se cumpla con los requisitos establecidos y las expectativas de cada cliente. Para ello se realizan:
Inspección y pruebas periódicas durante el proceso de producción para detectar y garantizar que los productos cumplan con los estándares de calidad.
Auditorías de calidad regulares para evaluar y mejorar el sistema de gestión de calidad en su conjunto.
3.- Control de la producción en tiempo real
El control de la producción es un proceso clave en la gestión de la producción que permite revisar y regular todos los procesos de fabricación. Para garantizar que se realizan de forma óptima y manteniendo los más altos estándares de calidad.
Dicho control en tiempo real permitirá multiplicar los beneficios productivos, considerando desde la recolección de datos en tiempo real, la prevención de paradas en fábrica y la gestión de desechos entre otros aspectos de fabricación.
4.- Gestión de la Cadena de Suministro
Es clave dentro de la gestión de la producción, ya que la planificación de la cadena de suministro permite la coordinación de los flujos de materiales y productos desde los proveedores hasta los clientes.
Gestión de stock e inventario: control constante de los niveles de stock e inventario para garantizar que se tengan suficientes materias primas y componentes para satisfacer la demanda, sin incurrir en excesos de inventario que puedan generar costos innecesarios.
Evaluación de proveedores: se evalúan y seleccionan proveedores basados en criterios como calidad, confiabilidad y costos. También se establecen acuerdos contractuales para asegurar el suministro continuo y los aspectos relacionados con la logística.
5.- Mantenimiento y sustitución de equipos y máquinas
Programación de mantenimiento preventivo: se establece un plan para equipos y maquinaria, lo que implica inspecciones y reparaciones programadas para evitar tiempos de inactividad no planificados.
Gestión de activos: se realiza un seguimiento de la vida útil de los activos de producción y se toman decisiones sobre la reparación, renovación o reemplazo de los equipos.
6.- Mejora continua
Gestión de procesos: se analiza de forma constante los procesos de producción en busca de ineficiencias, cuellos de botella y oportunidades de mejora. Se implementan cambios y se hacen ajustes para optimizar la eficiencia y la calidad.
Recopilación de datos sobre el desempeño de la producción y se utilizan para tomar decisiones basadas en datos. Esto incluye el uso de herramientas como el análisis de tendencias y la gestión de indicadores clave de rendimiento (KPI) en un cuadro de mandos.
7.- Gestión de proyectos
Definición de proyectos: se identifican proyectos específicos, como la expansión de una línea de producción o el lanzamiento de un nuevo producto. Se definen los objetivos, los plazos y los recursos necesarios.
Seguimiento constante para que los proyectos estén dentro del alcance, el presupuesto y el tiempo establecidos.
8.- Gestión de riesgos
Identificación de riesgos que puedan afectar a la producción, como la interrupción de la cadena de suministro o eventos inesperados.
Mitigación de riesgos identificados, lo que puede incluir la diversificación de proveedores, la implementación de plantes de contingencia o la inversión en tecnología de respaldo.
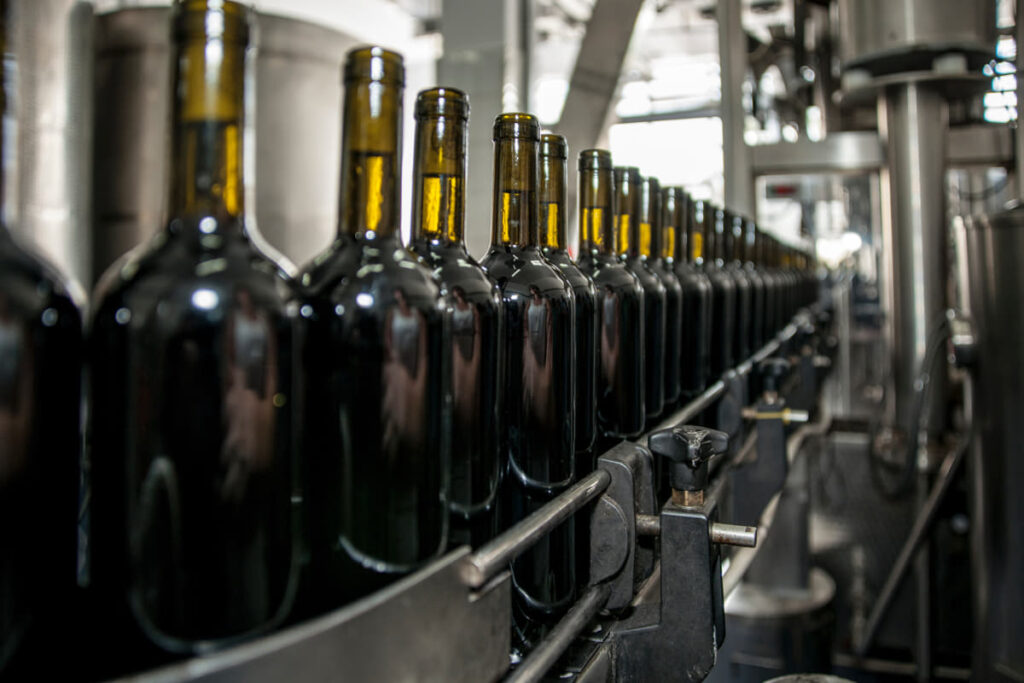
Aplicaciones para gestionar la producción
Existen aplicaciones, a nivel corporativo y ejecutivo, más destacadas para gestionar la producción de una compañía como son:
1.- Sistemas ERP (Enterprise Resource Planning)
Los sistemas ERP son aplicaciones integrales que abarcan múltiples aspectos de la gestión empresarial, incluyendo el ámbito de producción (para aquellas empresas que sean manufactureras).
Los ERP son sistemas de gestión empresarial que ayudan a coordinar y gestionar recursos, procesos y datos en toda la organización desde el aspecto financiero, compras-ventas hasta el productivo. En este punto es clave considerar la importancia de los sistemas MRP (Material Requirements Planning) que se utiliza para planificar y controlar el inventario, además de los materiales necesarios en el proceso de producción.
2.- Sistemas APS (Advanced Planning and Scheduling)
Los sistemas APS se centran principalmente en la planificación y programación avanzada de la producción, optimizando la asignación de recursos y la secuenciación de tareas.
Un sistema APS de planificación avanzada sirve para analizar los datos del proceso productivo de forma global y en tiempo real. Esto permite ser muy flexibles dentro del proceso productivo permitiendo responder al momento de las problemáticas que surjan en fábrica.
3.- Sistemas MES (Manufacturing Execution System)
Los sistemas MES supervisan y controlan las operaciones de producción en tiempo real, asegurando que se sigan los procesos y se recopilen datos precisos.
Este software es el elemento base de la digitalización de la producción. Un sistema MES es como el sistema ERP de la fábrica, ya que permite la gestión en tiempo real de lo que sucede a nivel productivo.
4.- Sistemas de Gestión de Calidad (Quality Manufacturing System)
Estos sistemas se utilizan para gestionar y documentar procesos de control de calidad, incluyendo la inspección de productos y la gestión de no conformidades.
A nivel más operativo, existen otros software que se utilizan a nivel del día a día en planta como la regulación de los sistemas de la maquinaria (PLC/PAC) y también considerar la interfaz con el proceso de producción vía sensores y actuadores (sensores/actuadores/hardware).
¿Cómo elegir un software MES?
Para que una empresa manufacturera pueda elegir adecuadamente un software MES ha de tener en cuenta unas consideraciones importantes como:
1.- Determinar las necesidades específicas de la empresa
Este aspecto es clave, ya que determinar qué necesita una empresa es muy importante para determinar el alcance del sistema MES y de qué es lo que necesita en cada fase del proceso productivo. Por ello, es clave realizar un análisis de qué necesidades tiene tu empresa en cuanto a la gestión de la producción.
Lo que implica considerar el tipo de productos que se fabrican, conocer cuales son tus procesos productivos, determinar qué sistemas de control utilizas y los KPI relevantes para tu negocio.
2.- La escalabilidad del software
Tanto en relación al sistema MES como a cualquier software dentro de la gestión empresarial y productiva de una compañía, es importante que el sistema sea escalable y pueda crecer a medida que lo haga tu empresa.
Además, debes ser capaz de adaptarse a cambios en la producción y en la organización, ya que la flexibilidad es clave dentro de un entorno empresarial productivo.
3.- Facilidad de integración
Hoy en día un software de una compañía no puede funcionar de forma aislada e independiente, es clave conocer la posibilidad de integración con otros software como ERP, sistemas de planificación y programación avanzada, sistemas de control de calidad, sistemas de automatización de fábrica y sistema de gestión de inventarios. La integración eficaz es esencial para una gestión de la producción fluida.
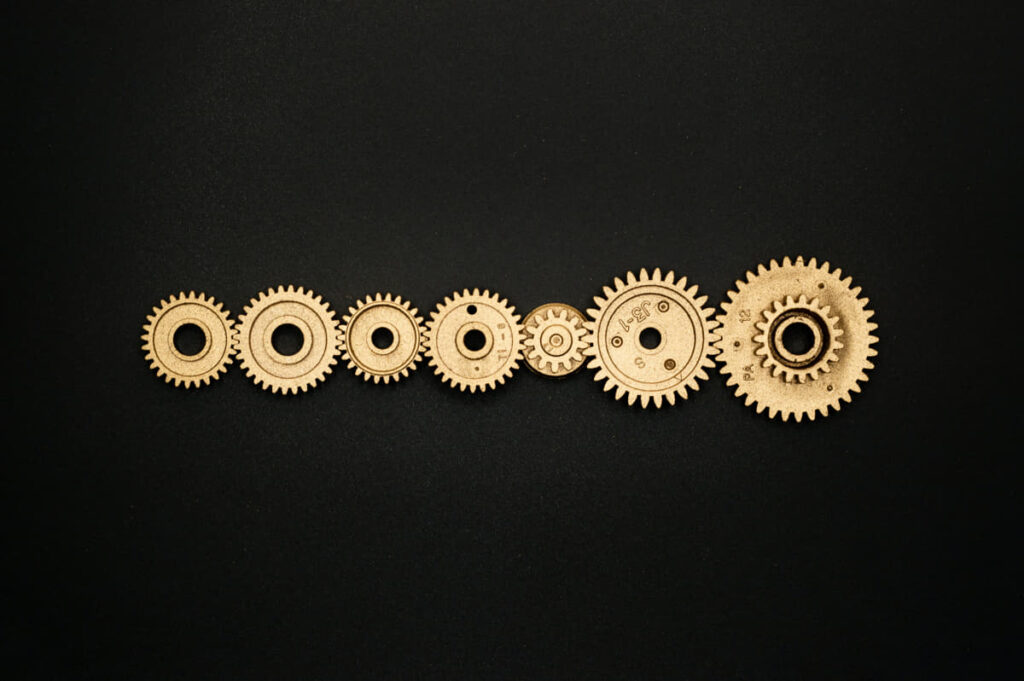
4.- Posibilidad de personalización
Es importante comprobar si el sistema MES que se elija tiene posibilidad de personalización/configuración a medida de las necesidades específicas de cada compañía. Cada empresa tiene procesos únicos y, por lo tanto, puede requerir configuraciones y flujos de trabajo personalizados.
5.- Experiencia de usuario
La interfaz de usuario, es decir, la facilidad de uso es importante. Asegurándonos de que la interfaz de usuario sea intuitiva y amigable, ya que será utilizada diariamente por el personal de la línea de producción.
6.- Capacidad de informes y análisis
Es importante evaluar la capacidad del sistema MES para generar informes y análisis de datos en tiempo real. Esto es esencial para la toma de decisiones informadas y la mejora continua.
7.- Seguridad y cumplimiento de estándares
El sistema MES debe cumplir con los estándares de seguridad y regulaciones aplicables a cada industria. Esto es particularmente importante en sectores altamente regulados, como la farmacéutica o la alimentaria.
8.- Soporte y servicio postventa
Te aconsejamos investigar la calidad del soporte técnico y los servicios postventa que ofrece el proveedor del sistema MES. Es importante estar seguro de que tendrás acceso a la asistencia técnica necesaria en el caso de surjan problemas con el software.
9.- Costos y ROI
El presupuesto será un elemento decisor acorde al presupuesto inicial que se tuviera. Evalúa los costos asociados a la implementación y mantenimiento del sistema MES, sí como el retorno de la inversión (ROI) que puedes esperar obtener a través de mejoras en la producción, eficiencia y calidad.
La elección de un sistema MES es un proceso crítico que requiere de una evaluación cuidadosa de las necesidades de la empresa y la selección de una solución que se ajuste a esas necesidades de manera eficiente y efectiva. La implementación exitosa de un sistema MES puede tener un impacto significativo en la eficiencia de la producción y la calidad del producto.